Causes of Drum Gear Coupling Failures
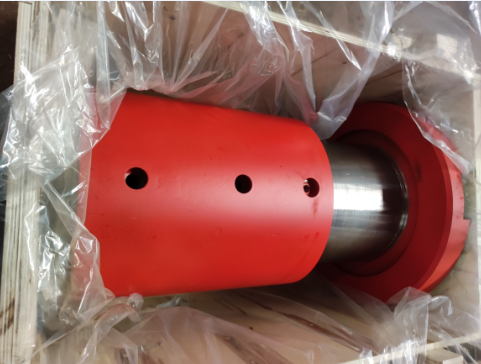
Causes of Drum Gear Coupling Failures
1. System Design & Integration Issues
· Unbalanced Shaft System Compatibility:
Components in the drive train (e.g., diesel engines, gearboxes, shafts, and highly elastic couplings) must be mutually complementary in design and application. Sub-optimal integration or low manufacturing precision in any component may compromise the entire system.
o Example: In marine applications, improper alignment between the main engine and propulsion system accelerates coupling wear.
2. Mechanical Overload & Misalignment
· Damper Subsidence in Prime Movers:
Subsidence of the main engine's vibration damper induces shaft misalignment, generating additional torsional loads.
o Consequence: Excessive heat buildup in highly elastic couplings leads to thermal stress fractures.
· Insufficient Compensation Capacity:
Despite their angular displacement tolerance, drum gear couplings may fail under unanticipated combined loads (e.g., simultaneous axial, radial, and angular stresses).
3. Operational & Maintenance Factors
· Improper Usage:
o Overloading beyond rated torque.
o Frequent starts/stops or reverse operations in non-design conditions.
· Environmental Neglect:
o Contamination (dust, moisture) entering unsealed lubrication cavities.
o Failure to replace degraded lubricant, accelerating tooth surface wear.
4. Industry-Specific Challenges
· Broad Application Scope:
Widely used in heavy industries (metallurgy, mining, etc.), couplings face diverse operational stresses.
o Risk: Misapplication in high-speed or ultra-precision scenarios beyond their design limits.
Key Takeaway:
Drum gear coupling failures often stem from systematic design flaws, mechanical over-stress, or operational oversights. Regular alignment checks, load monitoring, and adherence to lubrication protocols are critical for longevity.
https://www.timothyholding.com/Causes-of-Drum-Gear-Coupling-Failures.html